水泥生產方法
水泥的生產工藝簡單講便是兩磨一燒,即原料要經過采掘、破碎、磨細和混勻制成生料,生料經1450~C的高溫燒成熟料,熟料再經破碎,與石膏或其他混合材一起磨細成為水泥。由于生料制備有干濕之別,所以將生產方法分為濕法,半干法或半濕法,干法3種。
濕法生產特點
將生料制成含水32%一36%的料漿,在回轉窯內將生料漿烘干并燒成熟料。濕法制備料漿,粉磨能耗較低,約低30%,料漿容易混勻,生料成分穩定,有利于燒出高質量的熟料。但球磨機易磨件的鋼材消耗大,回轉窯的熟料單位熱耗比干法窯高2093~2931KT/kg(500—700kcal/kg),熟料出窯溫度較低,不宜燒高硅酸率和高鋁氧率的熟料。
半干法生產的特點
將干生料粉加10%~15%水制成料球入窯煅燒稱半干法,帶爐篦子加熱機的回轉窯又稱立波爾窯和立窯都是用半干法生產。國外還有一種將濕法制備的料漿用機械方法壓濾脫水,制成含水19%左右的泥段再入立波爾窯煅燒,稱為半濕法生產。半干法入窯物料的含水率降低了,窯的熟料單位熱耗也可比濕法降低837~1675kJ/kg(200~400kcal/kg)。由于用爐篦子加熱機代替部分回轉窯烘干料球,效率較高,回轉窯可以縮短,如按窯的單位容積產量計算可以提高2—3倍。但半干法要求生料應有一定的塑性,以便成球,使它的應用受到一定限制,加熱機機械故障多,在我國一般煅燒溫度較低,不宜燒高質量的熟料。
干法生產的特點
干法是將生料粉直接送入窯內煅燒,入窯生料的含水率一般僅1%~2%,省去了烘干生料所需的大量熱量。以前的干法生產使用的是中空回轉窯,窯內傳熱效率較低,尤其在耗熱量大的分解帶內,熱能得不到充分利用,以致干法中空窯的熱效率并沒有多少改善。干法制備的生料粉不易混合均勻,影響熟料質量,因此40—50年代濕法生產曾占主導地位。50年代出現了生料粉空氣攪拌技術和懸浮預熱技術,70年代初誕生了預分解技術,原料預均化及生料質量控制技術。現在干法生產完全可以制備出質量均勻的生料,新型的預分解窯已將生料粉的預熱和碳酸鹽分解都移到窯外在懸浮狀態下進行,熱效率高,減輕了回轉窯的負荷,不僅熱耗低使回轉窯的熱效率由濕法窯的30%左右提高到60%以上,又使窯的生產能力得以擴大。
水泥廠的主要工藝流程
水泥生產過程主要分為三個階段,即生料制備、熟料燒成和水泥粉磨。
以干法生產為例包括以下幾個主要工序:
破碎及預均化—生料制備—生料均化—預熱分解—水泥熟料的燒成—水泥粉磨—水泥包裝
1.破碎及預均化
(1)破碎水泥生產過程中,大部分原料需要進行破碎,如石灰石,黏土,鐵礦石及煤等。
(2)原料預均化技術就是在原料的存,取過程中,運用科學的堆取技術,實現原料的初步均化,使原料堆場同時具備貯存與均化的功能。
2.生料制備
水泥生產過程中,每生產一噸硅酸鹽水泥至少要粉磨3噸物料(包括各種原料,燃料,熟料,混合料,石膏),據統計,干法水泥作業生產線粉磨作業需要消耗的動力約占全場動力的60%以上,其中生料粉磨約占30%以上,煤磨占約3%,水泥粉磨約占40%。因此,合理選擇粉磨設備和工藝流程,優化工藝參數,正確操作,控制作業制度,對保證產品質量,降低能耗具有重大意義。
3.生料均化
新型干法水泥生產過程中,穩定入窖生料成分是穩定熟料燒成熱工制度的前提,生料均化系統起著穩定入窖生料成分的后一道把關作用。
4.預熱分解
把生料的預熱和部分分解由預熱器來完成,代替回轉窯部分功能,達到縮短回窯長度,同時使窯內以堆積狀態進行氣料換熱過程,移到預熱器內在懸浮狀態下進行,使生料能夠同窯內排出的熾熱氣體充分混合,增大了氣料接觸面積,傳熱速度快,熱交換效率高,達到提高窯系統生產效率、降低熟料燒成熱耗的目的。
(1)物料分散(2)氣固分離(3)預分解
5.水泥熟料的燒成
生料在旋風預熱器中完成預熱和預分解后,下一道工序是進入回轉窯中進行熟料的燒成。
在回轉窯中碳酸鹽進一步的迅速分解并發生一系列的固相反應,生成水泥熟料中的等礦物。隨著物料溫度升高近時,部分礦物會變成液相,溶解于液相進行反應生成大量 (熟料)。熟料燒成后,溫度開始降低。后由水泥熟料冷卻機將回轉窯卸出的高溫熟料冷卻到下游輸送、貯存庫和水泥粉磨所能承受的溫度,同時回收高溫熟料的顯熱,提高系統的熱效率和熟料質量。
6.水泥粉磨
水泥粉磨是水泥生產線制造的后工序,也是耗電多的工序。其主要功能在于將水泥熟料(及膠凝劑、性能調節材料等)粉磨至適宜的粒度(以細度、比表面積等表示),形成一定的顆粒級配,增大其水化面積,加速水化速度,滿足水泥漿體凝結、硬化要求。
7.水泥包裝
水泥出廠有袋裝和散裝兩種發運方式。
生產水泥設備
1.水泥窯系統
水泥窯是水泥廠的主要設備,由生料燒成熟料的整個過程都在窯內完成,簡單的回轉窯是干法中空窯。生料粉由窯尾加入,煤粉用一次風由窯頭噴入并在窯內燃燒,這里的火焰溫度達1800—2000℃。生料在窯內不斷向窯頭流動,濕度也逐漸升高,經過烘干、脫水、預熱、分解,到1300°C左右時出現液相,在火焰下面升高到1450°C燒成熟料,然后冷卻到1300~1100℃離開回轉窯落入單筒冷卻機,冷卻到100—150℃左右卸到熟料輸送機運至熟料破碎機,破碎后入庫貯存。
2.回轉窯系統
回轉窯是由鋼板卷制的圓筒,內砌耐火磚,由裝車簡體上的輪帶和下面的托輪支承,用裝在窯身上的大齒圈傳動。回轉窯通常以3.5%的斜度安放,轉數一般在1轉/分鐘以內、新式干法窯可達3轉/分鐘以上。單筒冷卻機與窯相似,不同的是筒內裝有揚料板用以加速熟料冷卻。窯頭高溫區簡體溫度過高,以前曾用水冷卻,現已改為用風冷卻。
上述干法中空窯是基本窯型,其他各種窯型主要是改變后部的烘干、預熱和分解部分的結構與型式,及變換熟料冷卻機。
3.水泥粉磨站
若把水泥生產設備工藝過程作為一個完整的工藝系統來看,終產品是水泥,熟料是半成品,所以可以將這個系統分開,從原料采掘到制成熟料是一段,由熟料制成水泥和裝運發貨是第二段。一般情況下這兩段應放在一起,這樣少占用土地,方便管理,用人工也少,可以完全集中控制。然而在有些特殊情況又以分開更為有利。
4.粉磨系統
球磨機是水泥生產工業早使用的粉磨設備,現在仍占主導地位,雖然它的效率很低,如按單顆粒的粉碎功耗計算只有6%~9%,但球磨機維護簡單,可靠性高,尤其用于水泥熟料粉磨,產品顆粒形狀和級配合適,水泥性能好,目前還難以找到可以完全取代的設備。
一:生料的準備
l 1.石灰石板式喂料機
l 布置位置 位于石灰石破碎車間內
l 用 途 用于石灰石喂料
l 2.石灰石破碎機
l 用 途 用于破碎石灰石
l 布置位置 位于廠區石灰石破碎車間
l 破碎型式 單段錘式(PCF20.18)
l 3.石灰石混勻堆取料機
二:生料磨制
球磨機
立磨機
4. 輥式磨
5.窯尾袋收塵器
規格型號 戶外型
用 途 用于窯尾及原料磨廢氣生料粉的捕集
布置位置 位于增濕塔與原料磨后面
6.窯尾袋收塵器排風機
用途 用于窯尾及原料磨系統廢氣處理
布置位置 位于窯尾袋收塵后
工作風溫 正常: 80~150℃ 極限溫度:200℃
7.窯尾高溫風機
用途 用于抽引預熱器廢氣
布置位置 位于預熱器后面、增濕塔后面
工作風溫 正常溫度:320~350℃;
極限溫度:450℃;
風機葉片需采用優質耐磨材料制成,保證轉子葉片有較長的壽命。
8.原料磨循環風機
用途 用于原料磨系統通風
布置位置 位于原料磨組合式旋風筒后
工作風溫 正常:90~100℃ 極限溫度(短時):250℃
風機葉片需采用優質耐磨材料制成,保證轉子葉片有較長的壽命。
三:熟料燒制
分解爐
預熱器
把生料的預熱和部分分解由預熱器來完成,代替回轉窯部分功能,達到縮短回窯長度,同時使窯內以堆積狀態進行氣料換熱過程,移到預熱器內在懸浮狀態下進行,使生料能夠同窯內排出的熾熱氣體充分混合,增大了氣料接觸面積,傳熱速度快,熱交換效率高,達到提高窯系統生產效率、降低熟料燒成熱耗的目的。
9.入庫斗式提升機
用 途 生料入庫(戶外型帶頭部檢修平臺)
10.入窯斗式提升機
用 途 生料入預熱器(戶外型帶頭部檢修平臺)
11.回轉窯
12. 篦式冷卻機
13.篦冷機冷卻風機
用途及位置 用于篦冷機廢氣供風,布置在篦冷機周圍
14.窯頭電收塵器
用 途 用于窯頭篦冷機余風處理
布置位置 位于冷卻機后面、窯頭電收塵排風機前面
15.窯頭電收塵排風機
用途 用于抽引冷卻機廢氣經電收塵器凈化后排空
布置位置 位于窯頭冷卻機和電收塵器后面
工作風溫 正常:200~250℃ 大(短時):400℃
風機葉片需采用優質耐磨材料制成,保證轉子葉片有較長的壽命。
16 熟料鏈斗輸送機
四:水泥磨制
17水泥磨粉站
18選粉機
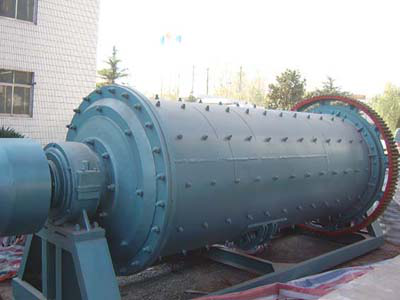